Inventory management has a crucial impact on the efficiency of enterprise operation. With the development of information technology and intelligence in manufacturing industry, more and more enterprises are using advanced technology to improve their inventory management. Taking FAW-VOLKSWAGEN Foshan Factory as an example, this paper aims to explore the main problems faced in the inventory management process, and study how to optimize inventory management with the help of modern logistics technology, and use digital, automated and intelligent methods to overcome the limitations of traditional management models, so as to achieve a more scientific and efficient inventory management system.
At present, the automobile manufacturing industry is facing a severe test, "high quality, low cost" has become the direction of traditional automobile manufacturers. Effective inventory management not only helps to reduce the inventory cost of enterprises,but also accelerates the flow of funds. Therefore, traditional automobile enterprises urgently need to innovate through the informationization of inventory management, adopt new technologies to replace traditional management methods, so as to reduce the consumption of human resources, reduce the risk of information errors and delays, and ensure that the inventory and varieties match the actual demand. So as to continuously improve the inventory management system and improve the overall management level.
Car production plants handle more than 10,000 parts. In inventory management, recei and warehousing is a crucial link, which involves the quantity and quality inspection, identification and information recording of goods, which directly affects the reliability of inventory and the timeliness of data update.
The traditional way of recei goods in storage relies on manual scanning of barcodes, which requires a series of steps such as stamping,scanning and tearing kanban labels, which not only causes a lot of wasted action and process waiting time, but also can lead to a long time of parts in the entrance, and even cause a backlog, which cannot be quickly stored. In addition, due to the complex process of recei goods and warehousing, it is necessary to manually complete multiple processes such as order receipt, recei, inspection, and shel,resulting in a long warehousing cycle and easy to miss or missweep, thereby distorting inventory information and increasing the risk of inventory management.
In order to solve these problems, many automotive factories have introduced RFID technology to optimize the recei and warehousing process. The specific practice is to bind an RFID tag to the bar code of the Kanban of the part, and fix it to the appliance or transfer vehicle that ships the part. When the forklift carries the equipment loaded parts through the discharge port, the ground sensor will trigger the RFID reader to read the label information, and send the radio frequency signal, the decoded information will be transmitted to the management system, and automatically create the storage record of the parts and its equipment, realizing the automatic storage registration when unloading.
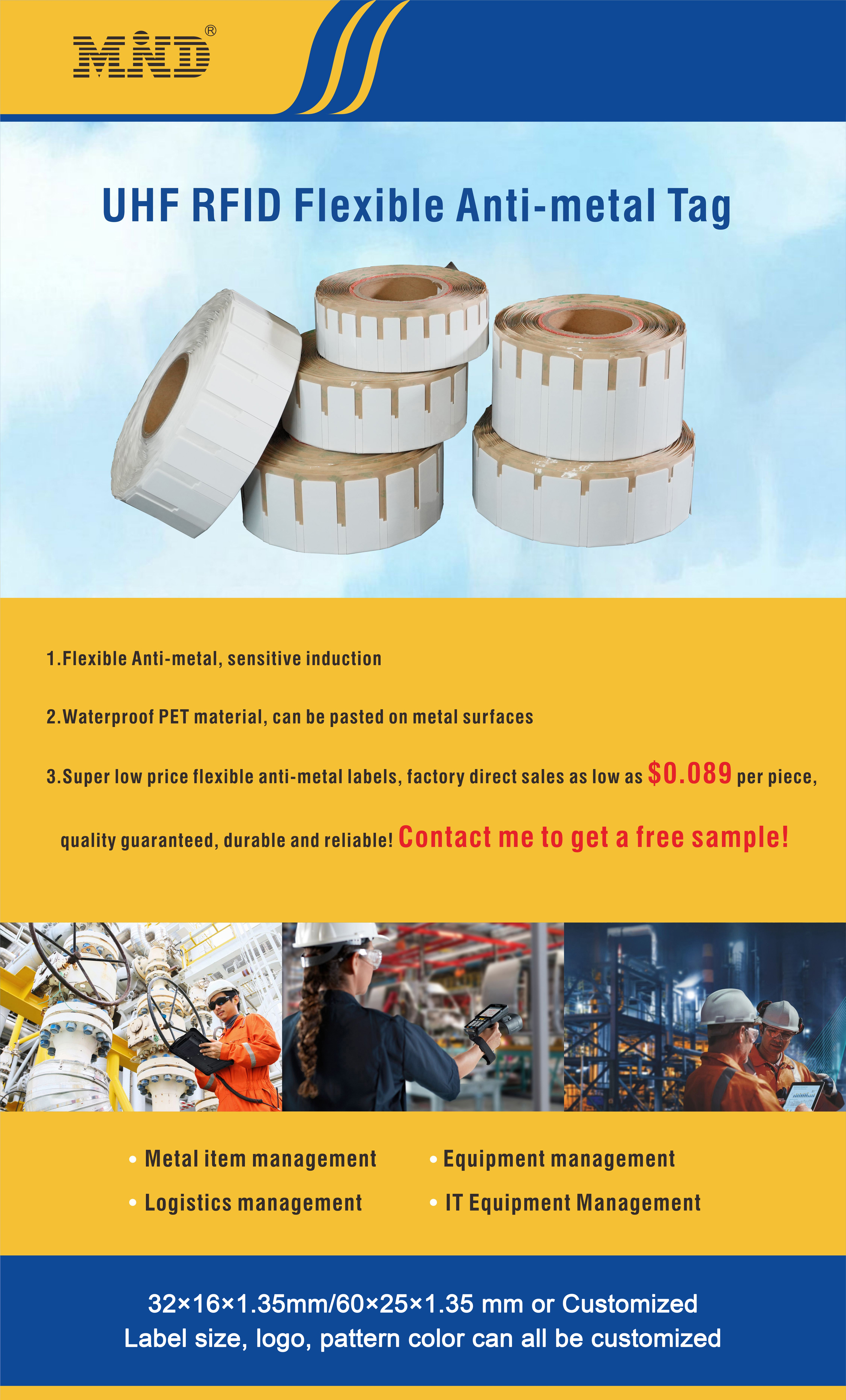
Post time: Sep-08-2024